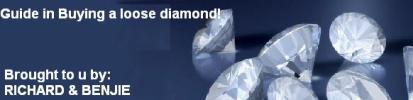
Diamond Information
Eighty percent of the diamonds mined annually are used
in industry; 4 times that production is grown synthetically for industry - that's a total of over 500 million carats or 100
metric tons. Diamond is a fundamental industrial material that affects our daily lives. Because diamond is the hardest substance,
it is used to cut, grind, and polish most hard substances. It fashions stones, ceramics, metals, and concrete, as well as
eyeglasses, gems, and computer chips. Its growing specialty-uses include blades, some used in critical surgery; specialty
windows; and heat spreaders. And of course diamond phonograph needles reproduced music for 50 years.
A diamond cutting tool shapes the armature of a generator.
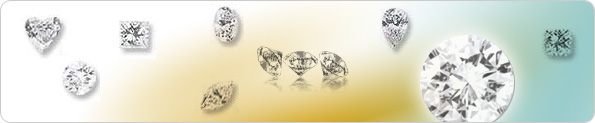
Diamond has three primary roles in industry: it is used
as a cutting tool, it is imbedded in another material and used as a tool or abrasive, and it is turned to powder or paste
for grinding and polishing. Diamond is selected for such use where its hardness and resistance to abrasion - its long working
life and fast cutting action - outweigh its costs. Moreover, diamond's resistance to wear enables it to cut reproducibly time
after time, a requirement of automated production. Diamond machining tools for turning, milling, and boring are preferred
where finely finished surfaces of high precision are needed. Diamond is used for machining a wide variety of plastics, glasses,
and metals, shaping products such as the drums for copying machines, polygon mirrors in laser printers, and aluminum-alloy
pistons in automobile engines. However, diamond cannot be used for machining alloys of iron. Under intense machining conditions
the diamond abrades very quickly against some materials, apparently because of a high-temperature reaction between iron and
carbon.
The device used by GE to synthesize diamond was termed
a belt device because tungsten carbide rams were driven into a cavity contained by a doubly-tapered carbide cylinder, contained
in turn by a steel jacket - termed a belt. Between the rams is a cylinder of graphite - a furnace - containing the material
to be raised to high temperature and pressure. Around the furnace assembly and between the anvils and belt is a compressible
material to contain the pressure and accept the deformation; it has traditionally been a natural clay called "pipestone clay"
for its alternative use in tobacco pipes. A hydraulic press, capable of perhaps 50 tons, drives the rams into the belt cavity,
amplifying the force at the interior to high pressure. An electrical current is passed between the rams and through the conductive
graphite, which heats in response; the clay acts as a thermal insulator as well as a container for pressure.
Research Using Diamonds Because of their transparency, thermal conductivity, or surface
properties, diamonds are used in many research instruments as windows. An application of exceptional value in mineral and
material science is a small device that generates extremely great pressures in the space between two diamonds - the diamond
anvil cell. These devices are used in experiments on the nature of planetary interiors and dense matter, from mimicking Earth's
core to producing solid hydrogen.
Alvin Van Valkenburg, pictured here in 1963, was a pioneer
in using the diamond anvil cell to study materials at high pressure at the National Bureau of Standards, Washington DC.
The mechanics of creating high pressure are simple, involving
just an application of force onto a small area, but extreme pressure will not be achieved without a material of supreme hardness,
incompressibility, and strength - such as diamond. Most materials, steel for example, will deform or break before reaching
pressures that exist deep within Earth. Tungsten carbide is better, but diamond is best. By polishing the ends off two fine
round brilliant diamonds to a width of a millimeter or so, and carefully and accurately squeezing them together, pressures
comparable to the center of Earth - 4,500,000 atmospheres - can be achieved. At these pressures hydrogen transforms into a
metal - a state that might exist deep within Jupiter. Research on planetary interiors and dense matter has been advanced greatly
by the use of diamond anvil cells, using lasers, optics, and x-rays to probe these small samples to reveal their mysteries.
Diamond Handling Heat, Friction and
Light Hardness is not the
only superlative property of diamond that makes it important in industry and technology--its extraordinary thermal conductivity,
low-friction surface, and optical transparency put diamond into cutting-edge applications. Many new products, like compact
electronic devices, windows for optical devices in demanding environments, and "no-wear" bearings, such as in the space shuttle,
utilize diamond. For these applications, a synthetic form leads the way. This is CVD, so-named for the growth technique chemical
vapor deposition.
Various products are composed of or coated with CVD diamond.
They include heat spreaders, cutting tools, windows, and bearings used in the space shuttle.
At present the major commercial application for CVD diamond
is in thermal management, where diamond heat-spreaders conduct byproduct heat away from a device. The material can be grown
with a thermal conductivity close to that of the best natural and high-pressure synthetic diamonds used until now as heat
spreaders. Thousands of suitable heat spreaders can be cut from a single wafer of CVD diamond, making for efficient use. A
CVD diamond coating on an object can be polished to yield an extremely smooth diamond surface, ideal for high precision and
low friction, such as is needed for precision bearings. CVD diamond wafers with high optical transparency are excellent for
viewing a wide portion of the electromagnetic spectrum in environments with extreme temperature, corrosiveness, or radiation.
Growing Diamonds Diamond was discovered to be carbon in 1796, and it took more
than 150 years from that time until a method of diamond synthesis was invented. The secret was pursued by many scientists
but not unlocked until the 1950s, when diamond was synthesized almost simultaneously by Swedish and American researchers.
Pressures of over 55,000 atmospheres and 1400C, plus molten iron to facilitate the change from graphite to diamond, were necessary.
Now some 80 tons of synthetic diamonds are produced annually by General Electric, De Beers, and many others for industrial
firms.
Herbert Strong and J. E. Cheney worked on GE's then new
1,000-ton press, capable of achieving experimental pressures of 100,000 atmospheres, in 1955. The GE team used the press to
grow diamonds prior to the announcement of diamond synthesis on February 15, 1955.
From the time Smithson Tennant showed that diamond was
carbon, experimenters tried to synthesize diamond from graphite or lamp black. Attempts over the next 150 years were all fruitless,
although the trend toward experiments at high pressure and temperature were in the right direction. The invention of tungsten
carbide in the 1930s provided a material that could achieve the pressure containment necessary for growing diamond. Experiments
in the 1940s by Harvard professor Percy Bridgman were unsuccessful, but finally in the early 1950s two teams succeeded. The
first was led by Baltazar von Platen, at the Allmanna Svenska Elektriska Aktiebolaget (ASEA) Laboratory in Stockholm, Sweden, in 1953, but this initial
success was not publicized or published. Thus, on February 15, 1955, the General Electric team of Francis Bundy, Tracy Hall,
Herbert Strong, and Robert Wentorf claimed credit for the first reproducible transformation of graphite to diamond. GE went
on to become the largest producer of synthetic diamond; De Beers follows, with many other manufacturers also contributing
to the annual output of synthesized diamonds.
Into the Future of Diamonds and Gems As methods for growing diamond, both at high pressure and by chemical
vapor deposition, improve, and as science finds ways to take advantage of diamond's properties, the potential applications
of diamond's superlative properties appear boundless. From super electronics, to indomitable optical windows, to unscratchable
surfaces - maybe the next watch bezel - diamond is an obvious choice.
Managing heat, particularly in electronics, with large
layers of CVD diamond is a rapidly expanding field. One of the most imaginative of these is the three-dimensional multi-chip
module, which holds out the promise of an extremely powerful supercomputer. To gain speed, electronics need to be as compact
as possible, concentrating waste heat as well. By stacking sandwiches of electronics and CVD diamond, a supercomputer could
be made small and cool enough to function. Diamond windows for infrared devices are under development and should find their
way into the tough environment of laser-guided smart bombs and more constructive uses in industry as well. The use of diamonds
as radiation detectors, light emitters in electronic displays, and coatings to make surfaces indomitable or unwettable are
being researched now. Beyond their imprint as a tool, diamonds will be showing up in more and more products in the future,
probably in your home electronics, appliances, and automobiles.
|